12月に入り寒さが日に日に増して、暖房器具が活躍する季節が
やってきました。
衣替え、車のタイヤ交換、ストーブやファンヒータの手入れなど
冬本場に向けてやることがたくさんありますよね。
柏崎事業所では冬場に備えて工場・事務所の雪囲いをしました。
雪囲いは昔ながらの手法ですが、積雪の重みを防ぐのと暴風や
冷気防ぐにも効果的です。
昨シーズンでは、雪囲いが破損するほどの大雪でしたが、
今シーズンは平均並みな降雪量であってほしいですね。
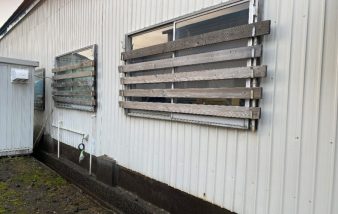
12月に入り寒さが日に日に増して、暖房器具が活躍する季節が
やってきました。
衣替え、車のタイヤ交換、ストーブやファンヒータの手入れなど
冬本場に向けてやることがたくさんありますよね。
柏崎事業所では冬場に備えて工場・事務所の雪囲いをしました。
雪囲いは昔ながらの手法ですが、積雪の重みを防ぐのと暴風や
冷気防ぐにも効果的です。
昨シーズンでは、雪囲いが破損するほどの大雪でしたが、
今シーズンは平均並みな降雪量であってほしいですね。
早いもので師走を迎えました。
今年もコロナ禍の一年でしたが如何お過ごしでしょうか?
昨シーズンは12月から大雪に見舞われて大変でしたが、
今年はどうなるでしょうか?
その雪に備えるべく、工場の外回りを良く見渡すと
インフラ設備に虫が食った様な跡が!!
これはいけないと思い補修をしました。
エアコンの室外機、灯油タンク等の外観を弊社の専門職の
皆さんに協力頂き驚くほどきれいに仕上げてもらいました。
これで大雪にも負けずに来春が迎えられると思います。
皆様も良いお年をお迎えください。
本日、この文章はお休みの日曜日に書いております。寒い外へ出る勇気が
なく、コタツの中からYouTubeの動画を見る一日。こんな日があってもよ
いのかなと考えながらダラダラ過ごしております。
そんな中で今日ハマったのは、最近何かと話題の北海道日本ハムファイタ
ーズのBIGBOSSこと、新庄剛志監督。なんと私と同い年の49才、誕生
日もたったの4日違いとのこと。なにせその生き方と話の面白さにたくさ
ん動画を見てしまいました。
新庄監督は、派手なパフォーマンスばかりが注目されがちですが、YouTube
の動画をチェックしていると、周りの人への気遣いや、当然ですが野球の
技術論への造詣の深さを感じます。(すいません、私は野球の素人ですが感
じたままの感想です。)
一番印象に残ったのは、守備についているとき、ピッチャーがボールを投
げるその瞬間の心の姿勢、気持ちの持ち方の話です。新庄監督はセンター
のポジションを守っていた現役当時、その瞬間、「内野ゴロも、ライトへ
の打球もレフトへの打球も全部俺がとってやる!」と考えていたそうです。
それくらいの気持ちが良いプレーにつながるのだと。
会社も野球と同様にチームプレーで、一人の力でできることは現実的には
限られていますがそれでも、「俺がやってやる!」という気持ちは大切だと
思います。誰のせいにもしないで、自分がやってやるんだという気持ちは、
強いパワーを生むのだと思います。
俺がやってやる!
と、今月はコタツの中からお送りしました。
11月2日に本社では「統計」の勉強会が開かれました。
今まで製作してきた製品の欠陥を集計し、どんなものが欠陥が出やすいかについて
話し合いをしました。
板厚によって出やすいものもあれば、製作部材によっても変わってきます。
また徐々に欠陥が減っているのもグラフ表されているため、自分たちが成長している
ことも見て取れます。
どんなところでミスが多いのか知り、気を付けることでさらに私たちの成長につなげて
いきたいと感じました。
「残業って何時間位するもんなんですか?」
先日、社内で残業のことについて話をしていた時にふと、もう25年も前
に、学校を卒業し田村製作所に戻るまでお世話になった川鉄建材(株)様
(現JFEシビル(株))の独身寮で、同室だった先輩にした質問を思い出し
ました。
「仕事ってそういうものじゃないねん。」(←下手な関西弁でスイマセン。)
との答え。仕事とは責任を果たすことであり、時間云々ではないのだと気
づかされた大切な思い出です。
もちろんワークライフバランスの実現において、残業時間が極力少ない労
働環境を作ることは会社にとって非常に大切です。しかしそれによってこ
れからの会社、社会をになう若手社員が仕事というものの本当の定義を勘
違いしてしまっては本末転倒だと感じます。
時間で仕事をすれば時間に縛られる。不自由です。しかし、仕事に責任を
もち実力をつければ、「今週忙しいけど、木曜日まで頑張って仕事を早く
進めて金曜日は友達と遊びに行くぞ!」と自分で決められるようになりま
す。自由になる、コントロールできるようになるのです。
同じ時間を過ごしても、両者の持つ時間の意味は全く違います。それは自
分自身にとっても、一緒に働く仲間たちにとってもそうだと思います。ぜ
ひわが社の若手社員たちには、私と同じように大きな気づきを得る、大切
な思い出を作ってもらえたらと思います。
梁、柱等、組立加工後には本溶接を行います。 その溶接時の熱で鋼材が縮んでしまうため、母材には、縮み代を設け、組立の時は、 設計値よりやや大きめになるよう組立加工をしています。 その縮み代ですが、柱一本の組立をして行く際には、ベース取り付け、コア組立、 仕口組立等複数の工程があり、また、コラム柱では、母材のサイズ、板厚によっても 変わってきます。そのため、柱大組後の溶接時にどの程度必要になるかを物件の初めの 一本目で縮み代の調整・確認をしながら加工をしています。 しかし、このやり方ですと、どうしても前半と後半とで、誤差ではありますが、 柱寸法にばらつきが出てしまいます。 そこで、柱母材のサイズ、板厚ごとに組立時の寸法とその溶接後の寸法のデータを取り、 設計値に対しての誤差として表記した一覧を作成していくこととしました。 現在、データ取りの最中ですので、まだ形にはなっていませんが、一覧ができれば、 物件内での製品のばらつきが抑えられると考えられます。 より良い製品を作れるよう、精進していきたいと思います。
弊社は10月20日が決算で、21日より新しい期が始まります。毎期、そ
の年の課題を一言で表し経営方針としています。来期の経営方針は、
『 先手の段取り、納得して仕事! 』
としました。
今年一年を振り返ってみると、色々な問題・トラブルの原因は何か事が起
こった時や状況に変化があった時にすぐに対応し、段取りをしていないこ
とにありました。新しい仕事を受注したり、何か事が起こったら、すぐに
先にどのような結果を作るかを見えてくるまで考えて、段取りをやり切る
ことが大切だと実感しています。
そして段取りを決めたら、その意味・意図をしっかり関係者に共有し、納
得して仕事をすること。そんな意図をこの経営方針に込めました。
本当はSDGsとかDXとか恰好を付けて書きたいところですが、それを書
けばなんだかウソになってしまいそうで。
しかし、仕事の段取りをしっかりとし、皆で納得してトラブルなく仕事を
進めることは、お客様にご迷惑をおかけせずに仕事を全うすることであり
、従業員の働きやすい労働環境を作り出すことでもあります。そして弊社
が引き続き存在することで、本当に微力ながらも社会の力になっていく。
そこからでよいのではないかと思っています。
というわけで皆様にご迷惑をおかけしながらも頑張っていきたく思います。
引き続きどうぞよろしくお願いいたします。
昨年に引き続きコロナ禍で歓迎会・懇親会ができない状況ですので、
仕事を円滑に進めるためにも、各事業所から新人社員さん同士の
コミュニケーションの場を設けました。
自己PRを始め、自身の業務内容の紹介や入社してからの意見も
お聞きし、普段仕事で関わることがない人の性格や考え方がわかり、
とてもいい機会になりました。
また、今回の意見交換会で会社の社員としての自覚を持っていただきたく
“サッカーチーム”をイメージしてお話ししました。
いいプレーが出来るように声を掛け合います。
ゴールしたら一緒に喜びあう、もし誰かがミスしたとしても、
カバーし励ましあう、いろいろな役割があってチームが成立します。
新人社員の皆さんには自分はどう動いたらいいかチームのメンバーに
どう声を掛けたら自分のチームがよくなるか考えて行動してもらいたいです。
田村製作所では10月に第56期の期末を迎えます。
今期を通して、本社では28件、柏崎事業所では29件の起案がありました。
内容を振り返ってみると、工場内の設備や機器などについての起案が
多くみられたように思います。
例えば、
製品移動時に製品を傷付けないよう、新しいスリングを導入しました。
フォークリフトのパレットに落下防止用の枠を作りました。
梁などの製品を積み上げる際に使用する台木用のラックを作りました。
どの改善も廃材を利用するなどして工夫を凝らしています。
工場での作業性をUPさせることはもちろんのこと、
お客様へお届けする製品をきれいに仕上げることにつながる改善と
なっています。
10月21日からスタートする来期も、たくさんの改善起案により、
よい製品をお客様へお届けできるような社内のアイディアや工夫が
出てくるといいなとおもいます。
実は今期の田村製作所では会社ホームページをリニューアルしようと奮闘していました。
恥ずかしい話、ホームページとして機能していないページもあったり、
古い作業着のままの従業員が映っていたり、なんてことが発覚しリニューアルすることに。
ホームページを新しくすることで田村製作所をもっとよく知ってもらいたいと思っています。
これまでは施工実績を写真と共に紹介したり会社情報の更新をしてきました。
そして今月はホームページとパンフレットの写真をプロのカメラマンさんに依頼!
1日かけて本社、柏崎事業所の2ヵ所で写真を撮って頂きました。
今回の写真は素人の写真になりますが、
来期(10月決算なので11月)になるとNEWホームページ、NEWパンフレットに変わります。
その時はぜひ覗いてみてください。